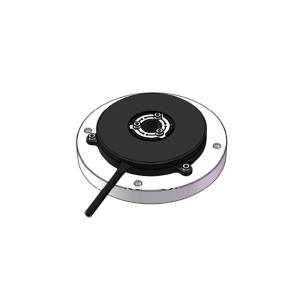
Add to Cart
High Precision Induction Encoder Resistance To Dust Water And Oil Pollution
High Precision Induction Encoder Resistance To Dust Water And Oil Pollution
1. Product overview
Inductive encoder is composed of excitation coil, induction coil and code disk reflector.
The code disk reflector causes magnetic field deflection, and the deflection angle is different at different positions.
The differential induction coil induces the voltage signal associated with the code disk position. The encoder analysis circuit is composed of precision excitation circuit, induction signal collection circuit, high-speed synchronous rectification current, amplification and conditioning circuit, analysis circuit, communication circuit, etc. the sine and cosine induction circuit is composed of two groups of sensor circuits, each group of which is composed of differential sine and cosine.
The two groups of sensor circuits have mutually prime cycle numbers, which can identify the absolute zero position of a single turn and can have partial self-correction function.
The accuracy of inductive encoder is related to its induction principle and diameter. The larger the diameter, the higher the accuracy can be achieved.
At the same time, since it has no bearing, the accuracy is also closely related to the installation. Especially important is the eccentricity of the encoder after installation and the radial runout of the measured shaft. After the inductive encoder is installed, there will be a certain deviation between the encoder and the shaft. In addition, the shaft size and shape error of the customer also increase the eccentricity error.
Eccentricity e, average diameter D of encoder rotor and measurement error ∆φ The relationship between:
∆ = measurement error, unit: angular second
e = eccentric error unit after encoder installation μM (1/2 radial runout)
D = average diameter of encoder, unit mm
M = encoder Center
φ = "Measured" angle
φ’= Measured angle
The encoder has the following characteristics:
1. Good environmental resistance, dust, water and oil resistance, low installation environment requirements, and no clean room installation and operation.
2. The inductive encoder is an area sensor (relative to a point sensor) and can tolerate a certain installation deviation.
3. Inductive encoder has high safety and has no enrichment effect on magnetic dust compared with magnetic sensor. It is widely used in key parts of automobile, military industry and aerospace fields.
4. The modulation characteristics of the inductive encoder can better suppress the 1 / f noise of the circuit, and the long-term stability of the position is good.
5. Inductive encoder, no fragile materials such as glass code disk, high seismic resistance.
6. Inductive encoder is suitable for low temperature environment.
2.Encoder specification
Integrated package
EIS 16 | EIS 25 | EIS 37 | EIS 40 | EIS 58 | EIs 9o | EIS 130 | |
External diameter | 16 | 25 | 37 | 40 | 58 | 90 | 130 |
Internal diameter | 4 | 6 | 10 | 10 | 20 | 50 | 90 |
Thickness(mm) | 8 | 7 | 8 | 10 | 10 | 10 | 10 |
Communication | RS485/Biss -C/SSl | ||||||
Maximum speed(rpm) | 6000 | 6000 | 4000 | 4000 | 4000 | 3000 | 1500 |
Resolution (bits) | 17 | 17/19 | 17/19 | 17/19 | 19/21/23 | 21/23 | 23 |
Package split type
EIF37 | EIF 58 | EIF 75 | EIF 90 | EIF 100 | EIF 125 | EIF 150 | EIF 300 | |
External diameter | 37 | 58 | 75 | 90 | 100 | 125 | 150 | 300 |
Internal diameter | 8 | 12.5 | 25 | 40 | 50 | 75 | 110 | 250 |
Thickness(mm) | 11.25 | 14.6 | 15.4 | 15.4 | 15.4 | 15.4 | 154 | 16.4 |
Communication | RS485/Biss -C/SSI | |||||||
Maximum speed(rpm) | 9000 | 9000 | 9000 | 7200 | 7200 | 6000 | 5000 | 4500 |
Resolution (bits) | 17/19 | 19/21/23 | 21/23 | 21/23 | 21/23 | 23 | 23 | 23 |
Open type
EIC25 | ElC40 | EIC 60 | EIlC 100 | |
External diameter | 25 | 40 | 60 | 100 |
Internal diameter | 10 | 15 | 25 | 50 |
Thickness(mm) | 6 | 6 | 6 | 8 |
Communication | RS485/Biss -C/SSl | |||
Maximum speed(rpm) | 6000 | 6000 | 4000 | 4000 |
Resolution (bits) | 17 | 19/21 | 21/23 | 23 |
3. Parameter table
General parameters | Electrical parameters | ||
Resolving power | 17 / 19 / 21 / 23 bits | Supply voltage | 5V main 5% |
System accuracy | 0.02 ° (standard) | Current consumption | 90mA |
Maximum allowable speed | 9000 rpm | Connector type | Shielded twisted pair |
Single turn / multi turn | Single lap | ||
Mechanical parameters | External environment | ||
Allowable installation eccentricity | 0.1mm | EMC standard | IEC6100-6-2/4 |
Allowable axial installation error | 0.1mm | Working temperature | -45°℃-+85°℃ |
Rotor inertia | 4.8E-O5 kgm2 | Storage temperature | -55°C-+125℃ |
Total weight | 150g | Humidity | 0~99% non condensing |
Od / ID / height | See specific specifications | To attack | 100g 11ms |
Material Science | Shell aluminum alloy | Shock | 20g 10-2000Hz |
Protection level | P65 |
4. Naming method
E | l | S | A- | 058- | S | 21 |
Type: I:inductive type | Packaging style: C: open packaging; | Occurrence mode: A: radial outgoing line 250mm (scattered line); B: radial outgoing line 500mm (scattered line); C: axial outgoing line 250mm (scattered line); C: axial outgoing line 500mm (scattered line) | Outer diameter dimension 25: 16-25mm | Model output S: SSI B: biss-c R: RS485 (compatible with NRZ) O: other | Resolution: 17:17bits, 19:19bits, 21:21bits, 23:23bits |
Factory environment